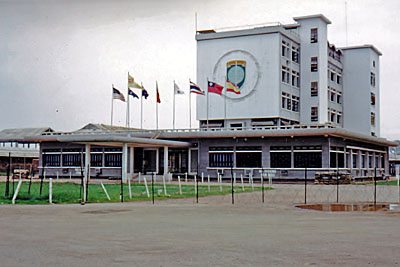
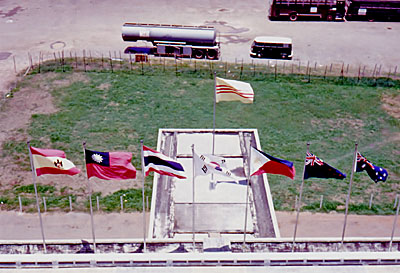
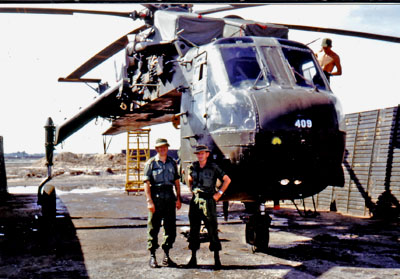

EQUIPMENT INSPECTION IN SOUTH VIETMAM
Reprint from the DEME (Aust) Liaison Letter No 50 of August 1969
Introduction
A RAEME Equipment Inspection Section (EIS) operates in South Vietnam. Its method of operating varies in some aspects to that practised by EIS in Australia. This is brought about because of theatre conditions, and limitations in manpower.This article describes the operation of the HQ AFV EIS during 1968. A description of the US Army system of carrying out unit technical inspections is also included for general interest.
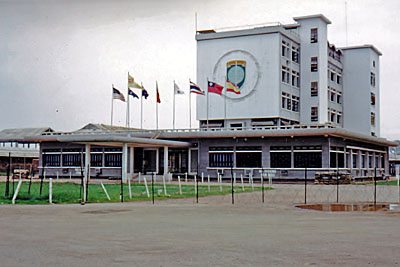
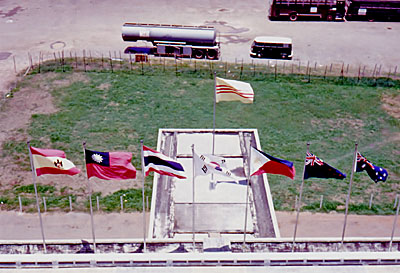
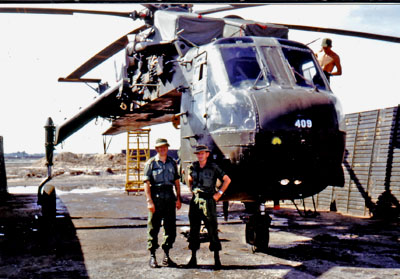
PART 1 - HQ AFV EIS
Command
The section is part of the QMG Branch at HQ AFV. A RAEME Capt commands the section under the technical direction of the DADEME HQ AFV.
Organization
The section has a headquarter at HQ AFV in Saigon and is organized to provide two sections to carry out the following types of inspection.
- Continuing inspections of B Vehicles throughout the theatre
- Continuing inspections of technical equipment other than B Vehicles throughout the theatre. These have been termed GE inspections
- Special inspections as directed by DADEME HQ AFV
Each inspection team consists of Warrant Officer assisted by an NCO tradesman. The teams are situated at either Saigon, 1 ATF or 1 ALSG for the duration of the inspection of each area. Inspection programmes are arranged so that the teams are never operating in the same area, together. This reduces disruption to units and provides inspectors in at least two locations to carry out special inspection tasks for DADEME if required.
Planning
Inspection timings and types are calculated and planned by the section OC at HQ AFV in conjunction with Q Branch HQ AFV. The allocation of inspection dates to specific units is arranged to conform with operational commitments by the Q Branch in the area being inspected.
Vehicle Inspections
Inspection of all B vehicles and trailers is carried out in each area. Vehicles are inspected at the rate of approximately five each day. At this rate it takes about six months to inspect all B vehicles in the theatre.
Vehicles are inspected to ASA standards with allowances being made for cleanliness and bodywork because of theatre/area conditions. Theatre policy on relaxation of standards of serviceability is decided by DADEME HQ AFV and EME 1 ATF and repair action on the inspection reports is governed by this policy.
Emphasis is placed on inspecting to assess the thoroughness of unit non-technical inspections, driver maintenance and service station technical inspections.
GE Inspections
The emphasis in GE inspections is placed on small arms and weapons. However, inspections are subdivided into GE, Instrument and Miscellaneous equipments and include inspection of all items of technical equipment held by the unit except telecommunications equipment. Many of the non-weapon equipments, e.g. typewriters, starlightscopes, are given a functional check and inspection for satisfactory operator servicing only. However, field cooking equipment, air compressors and many other equipments of a general nature are given a thorough technical inspection.
Special Inspections
Special inspections are performed on direction from DADEME HQ AFV and may vary from inspection of theatre holdings of major equipment, e.g. forklifts, generators to inspection to assist with defect investigation.
PART 2 - OBSERVATIONS
Flexibility
A degree of flexibility must be provided when planning inspections in an operational theatre. The operational commitments of units can be changed suddenly and without notice making it impossible to carry out inspections on the dates planned.
Weather conditions in South Vietnam have an influence on inspection schedules. As sheltered areas are not always available, allowances must be made for interruptions to the programme in the wet season.
Vehicle Inspections
Units are generally aware of their servicing and maintenance responsibilities towards vehicles. However, the requirement for unit servicing inspections (non-technical inspections) was not fully understood by all. A more definite method of recording these and subsequent follow up action should be provided than currently exists. This system should be standardized throughout the AMF, and should be incorporated in existing vehicle documents.
GE Inspections
Initial GE inspections revealed that very few units were aware that they had any responsibility towards inspection or maintenance of equipments such as typewriters, washing machines, lawn mowers, and other items not issued on a personal basis. Further, very few operators of equipment in this category had received any formal training except for basic operating. Although the responsibility for care and maintenance of technical equipment is defined in Equipment Instructions, it is felt that this is not specific enough in most cases. A suitable publication should be produced to clearly explain how units should inspect, operate and maintain each type of equipment it holds. The system should provide a standardized log book for all types of equipment and should permit recording of unit inspections and subsequent follow up action.
The GE inspections proved to be an extremely effective means of advising units of their responsibilities, and operators of the methods of inspecting and servicing their equipment.
Minor repairs to small arms and office equipment was carried out during inspection tours in Saigon. Equipment in the other areas was inspected only, repairs being carried out by local RAEME resources.
PART 3 - THE US ARMY SYSTEM
General
Several days were spent on detachment with the 1st Logistic Command (1st Log) Inspection Team operating from Long Binh. An outline of the US system follows for general interest.
The units of 1st Log are subjected to several forms of inspection. Inspections of both an administrative and technical nature are carried out by various levels of command. For example, the units in the Saigon Support Command area were subjected to annual Adjutant General's Inspections (AGIs) to assess all aspects of the unit's efficiency, and technical inspections, by both the unit's corps, and 1st Log teams, to assess their efficiency in relation to their technical equipment. The corps inspections are normally done as a preliminary to the other inspections to ensure units are at the requisite standard.
The inspection most resembling our own from the aspects of both command level and content is the Command Maintenance Management Inspection (CMMI). This inspection is designed to assess a unit's efficiency not only with respect to the state of its equipment, but also the unit's managerial functions relating to equipment maintenance. The detachment on which this article is based was with the 1st Log CMMI team operating in Saigon Support Command area.
Organization
The CMMI field team consisted of a Chief Warrant Officer (CWO) and a group (seven in this particular case) of specialist NCOs. The team was designed to assess units of company size in one day.
Units are subjected to CMMI once each year and must pass all aspects of the inspection. If a unit fails the inspection, reinspection takes place until either the unit passes or disciplinary action is taken. Regulations state that units may be given four hours notice prior to the inspection. 1st Log units were given about twelve hours notice for initial inspections and had no way of knowing the exact date of the inspection until notice was issued.
Conduct of the Inspection
The team arrives at the unit selected for inspection at the date and time advised. An entry briefing is given by the CWO and then each inspector is allocated a guide familiar with the various areas being inspected.
The inspectors then inspect a percentage of each type of the equipments in their specialist fields, (i.e.) vehicles, weapons, ammunition, etc. The quantity of each equipment inspected is based on fixed percentages prescribed for total numbers of equipment held. The items to be inspected are selected at random from the unit's total holding. Assessment is made of maintenance, storage and preservation, and is based on allocating prescribed points for the various equipments. The number of points possible for each equipment is prescribed in Army Regulations and is based on the degree of maintenance difficulty presented by the individual equipment, (e.g.) a rifle may be worth seven points if maintenance is perfect, whereas a bulldozer may be worth 200 points. Points are deducted for prescribed breaches in maintenance and are classified as either "shortcomings" or "deficiencies". Shortcomings being minor breaches, for which one point may be deducted, such as dust in the bore of a weapon, and a deficiency being a serious defect such as a broken locking shoulder. The marking guide for each equipment prescribes the shortcomings and deficiencies, and the number of points to be deducted from the possible total for detection of either. Normally, more that one deficiency on an equipment will cause disqualification of all points for that equipment.
Percentages based on the points gained and the number of equipments inspected is calculated by each inspector.
The CWO assesses the unit's maintenance management procedures related to unit inspection, servicing, operator training, documentation, repair procedures and replacement parts accounting. Units must be able to produce correctly compiled log books, proof that their prescribed holding of replacement parts is up to date, and their unit technical training programme is satisfactory.
The maintenance management phase of the inspection is particularly thorough. An examination of the unit entitlement and accounting documents is made. Surpluses or deficiencies in unit technical equipment are queried. Particular attention is placed on training of equipment operators within the unit. This is known as "On the Job Training" (OJT), and must be carried out in accordance with procedures and syllabi prescribed in Army Regulations. For example, if a unit has a forklift, a check is made to see if a suitably qualified operator is held on unit establishment. If not, and the unit claims OJT is being given, the syllabus will be examined, technical reference material included on the syllabus must be produced and the personnel undergoing OJT may questioned. If OJT is not being given, or the unit does not have the capability to operate an equipment it holds, the inspector may recommend withdrawal of the equipment from the unit.
When all aspects have been assessed, the team congregates, and a consolidated report is prepared. Separate percentages are calculated for the Maintenance and Management gradings. The draft report is then presented to the OC at an exit briefing. Major points noted are emphasized and discussed with the various members of the unit staff. Exit briefings may be made at either the unit's headquarters, or at the unit's corps headquarters in the area. The draft reports are then passed to CMMI headquarters for formal production and distribution. All failures are sighted personally by the Commanding General, 1st Log.
The responsibility for all aspects of the CMMI inspection is placed on the commander of the unit being inspected. His organizational maintenance element is completely his responsibility and, unlike our system, he is responsible for all aspects of its conduct.
Roadside Checks
The CMMI also carry out roadside checks of vehicles in their area. Roadblocks are set up and vehicles are stopped and inspected for roadworthiness and correct documentation. The number of vehicles to be inspected each month is issued as a policy by the formation commander and the CMMI team carries out the checks on a random basis between unit inspections.
Conclusion
The CMMI type inspection may sound harsh and "police like". However, when compared to many other US Army procedures it is not really severe. The team advises units in much the same manner as our EIS. The grading allocated to units is done on a purely impersonal basis according to regulations and is accepted by unit commanders as a fair assessment of their unit. A detachment with the CMMI is a worthwhile experience. Adoption of some of their techniques by the AMF would no doubt make units more aware of their technical maintenance responsibilities, and achieve a higher standard of equipment serviceability throughout the service.
End of Reprint
Author's Notes:
The above article is submitted for historical records only. Prior to May 1968, special technical inspections had been arranged in the South Vietnam theatre by the RAEME DADEME (Major J. A. McDonald) to assess the condition and locations of certain specific equipments, (e.g.) Telecommunications and certain C Vehicles. This was to gather information related to RAEME maintenance planning, and resource and manpower management. Also, B Vehicle inspections were carried out under the direction of Capt John Kingston (later Major General) to prove the concept and benefits of a full time EIS system operating in South Vietnam. Because of the success of these early inspections, a position of RAEME Inspector (Captain) was created in 1968 to arrange and supervise a regular EIS service in the theatre. This position was to be based at HQ AFV in Saigon.
Formal Establishment for the EIS Section only provided for the Captain OC. Therefore, the technical inspection teams had to be obtained from the manpower resources of existing RAEME units in theatre. This was not an easy task. The leaders of each of the Vehicle and GE Teams had to be an Artificer Warrant Officer. They were required to be very experienced in their trades, and have a conscientious approach to their duties. Also essential, was a personality suited to dealing with unit commanders and their staff at all levels. Because of the requirement to move and operate independently around the theatre, the team leaders also required a degree of initiative and resourcefulness developed to a much greater extent than that required to work in the normal RAEME unit environment. They also needed a tactful nature that enabled them to establish a rapport with unit management staff to convince them that they were there to help with their equipment servicing and maintenance responsibilities. Naturally, RAEME units with Warrant Officers with these technical and personal attributes were reluctant to let them go to be seconded to the EIS team. However, I understand that, after some "wheeling and dealing" between the DADEME staff and other RAEME officers in the theatre, suitable candidates were obtained to lead the two teams.
Before the first continuing, and 100 percent inspections could commence, it was necessary to obtain details of equipment held and where it was located in the various units in South Vietnam. This was done by circularizing all units and formations in the theatre. A schedule for the first inspection programme was then prepared and disseminated. I can only imagine how much easier this would have been today with the aid of computers.
The 100 percent Vehicle and GE EIS type inspections commenced around June, 1968. For historical records, the original two teams were:
- GE Team
- 41961 WO2 Robert Charles Thompson
- 1733028 Cfn Graham Douglas Perrin
- Vehicle Team
- 58510 WO2 Allan William Cook
- 29947 Sgt Reginald James Style
When the SVN EIS commenced, there was some resistance from local HQ and unit staff. This was because of their concern about yet another HQ AFV project requiring more of their precious time, and the extra "paper work" that would inevitably be created. However, because of the nature of the team's approach, units soon became aware that the EIS visits were designed to help them achieve better equipment serviceability, and how to use the RAEME theatre repair facilities to their advantage. I remember once visiting the 1st Australian Reinforcement Unit when the GE EIS team was inspecting the infantry soldier’s small arms. The troops had been out in the field, and the inspection team was waiting for them as they returned to their unit lines. The team was operating from a Field Service table out in the sun. The soldiers were mostly young national servicemen. Many who looked, to me, more like school cadets than soldiers being prepared for battle. They were all soaking wet from perspiration, and no doubt longing to get to the showers. However, the inspection team worked very efficiently, and quickly checked each weapon for outstanding modifications and serviceability. They also gave friendly advice and tips about cleaning and caring for their weapons. The soldiers were obviously impressed by the team's expertise, and the attention being shown to them and their individual weapons. They really showed their appreciation for the personal and friendly advice being given by these two RAEME people working like "Trojans" in the hot sun. I will always remember the looks of admiration on the faces of these young soldiers. This made it all worthwhile!!!
GLOSSARY OF TERMS
- 1 ALSG
- 1st Australian Logistic Support Group
- 1 ATF
- 1st Australian Task Force
- ASA
- Australian Support Area
- B Vehicles
- Non-armoured vehicles and excluding earth moving equipment and certain plant and construction vehicles
- C Vehicles
- Earth moving vehicles, Engineer Plant and Construction Vehicles
- DADEME
- Deputy Assistant Director of Electrical and Mechanical Engineering — senior EME Staff Officer, HQ Australian Force, Vietnam
- DEME
- Directorate of Electrical and Mechanical Engineering, Master General of Ordinance, Melbourne
- EIS
- Equipment Inspection Section
- EME
- Electrical & Mechanical Engineering
- Equipment Instructions
- The Army Manual that sets out the responsibilities and actions required to be taken by a Unit Commander to preserve the materiel with which he is issued, including it's usage, accounting, disposal, maintenance and servicing.
- GE
- General Engineering
- HQ AFV
- Headquarters Australian Force Vietnam
- NCO
- Non Commissioned Officer
- Q Branch
- Quartermaster Generals Branch.
- QMG
- Quartermaster General
- RAEME
- Royal Australian Electrical & Mechanical Engineers
- US
- United States of America.